July 10, 2023
According to the Federal Highway Administration, there are 4.2 million miles of roads and highways in the United States. Maintaining and upgrading them can be time-consuming and costly. As traffic volumes increase and infrastructure ages, innovative and cost-effective road rehabilitation techniques are needed. Full-depth reclamation (FDR) is a pavement rehabilitation technique to transform deteriorating road surfaces into durable, high-quality pavements.
FDR recycles existing pavement materials to create a stable and durable base for new road construction. It involves pulverizing the existing pavement and blending it with additives such as cement or asphalt emulsion. Once the additives are introduced and the new base layer is compacted, the new pavement surface materials can then be constructed on top of the blended and compacted base. While this method is commonly used to rehabilitate deteriorated asphalt pavements, FDR can also be used for granular roads and other types of pavement surfaces.
Benefits of FDR
There are many benefits of FDR, including cost and time savings, durability, and minimizing environmental impact.
Cost
Compared to traditional road construction methods, FDR techniques reuse existing materials, reduce disposal costs, lower maintenance expenses, and provide a longer service life. Using FDR compared to traditional removal and replacement methods, could generate a cost saving of over 50%.
Time
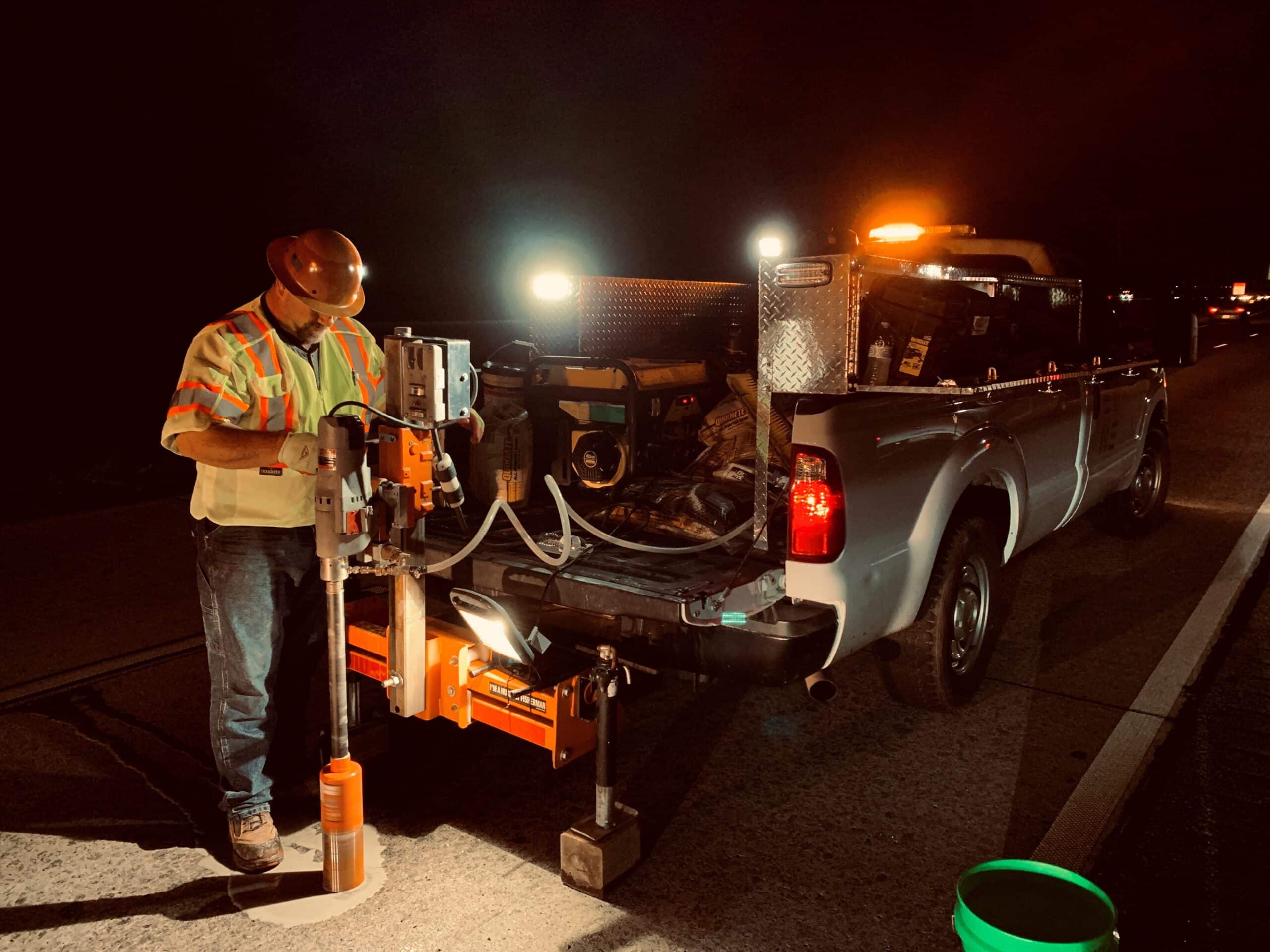
Traditional road construction methods often involve separate stages, such as milling, excavation, hauling, and disposal of old materials, followed by the transportation and placement of new materials. FDR streamlines these phases into a single operation, dramatically reducing the overall project timeline. Additionally, FDR minimizes traffic disruptions during construction by eliminating the need for multiple construction stages, traffic detours, and unnecessary road closures. This results in less stress on motorists and local communities, which is particularly beneficial for heavily congested areas or high-traffic roads where traffic flow must be maintained.
Improved Durability
FDR produces a robust road base that provides improved structural integrity. Incorporating stabilizing agents, such as cement or asphalt emulsion, enhances the strength and load-bearing capacity of the reclaimed material. As a result, the rehabilitated road becomes more resistant to rutting, cracking, and other forms of distress, leading to a longer service life. The increased durability of FDR-treated roads reduces the need for frequent maintenance, ultimately saving resources and reducing disruptions to traffic flow. This process also decreases the permeability of the new base, making it less susceptible to water penetration, a common cause of pavement deterioration. The stabilizing agent used in the process helps to bind the materials together, creating a more water-resistant structure that reduces the potential for potholes and base failure.
Section Upgrades
Pavement sections are typically designed and constructed in the most economical manner possible, with only the material thickness and quantities needed to support 15 to 20 years of presumed traffic. When new developments are constructed or when sudden increases in traffic occur, these changes result in added stress to the pavement. The added stresses will often result in premature cracking and heavy damage to roads that were not designed with new development in mind. FDR mixing can be extended 12+ inches below existing grades, so if a thicker road base is needed to upgrade an existing road, FDR is a viable alternative to traditional excavation and reconstruction methods.
Additionally, if widening, shoulder additions, or grade modifications are needed on existing roads, the blended materials can be easily shaped and graded to fit the required grade adjustments.
Environmental Benefits
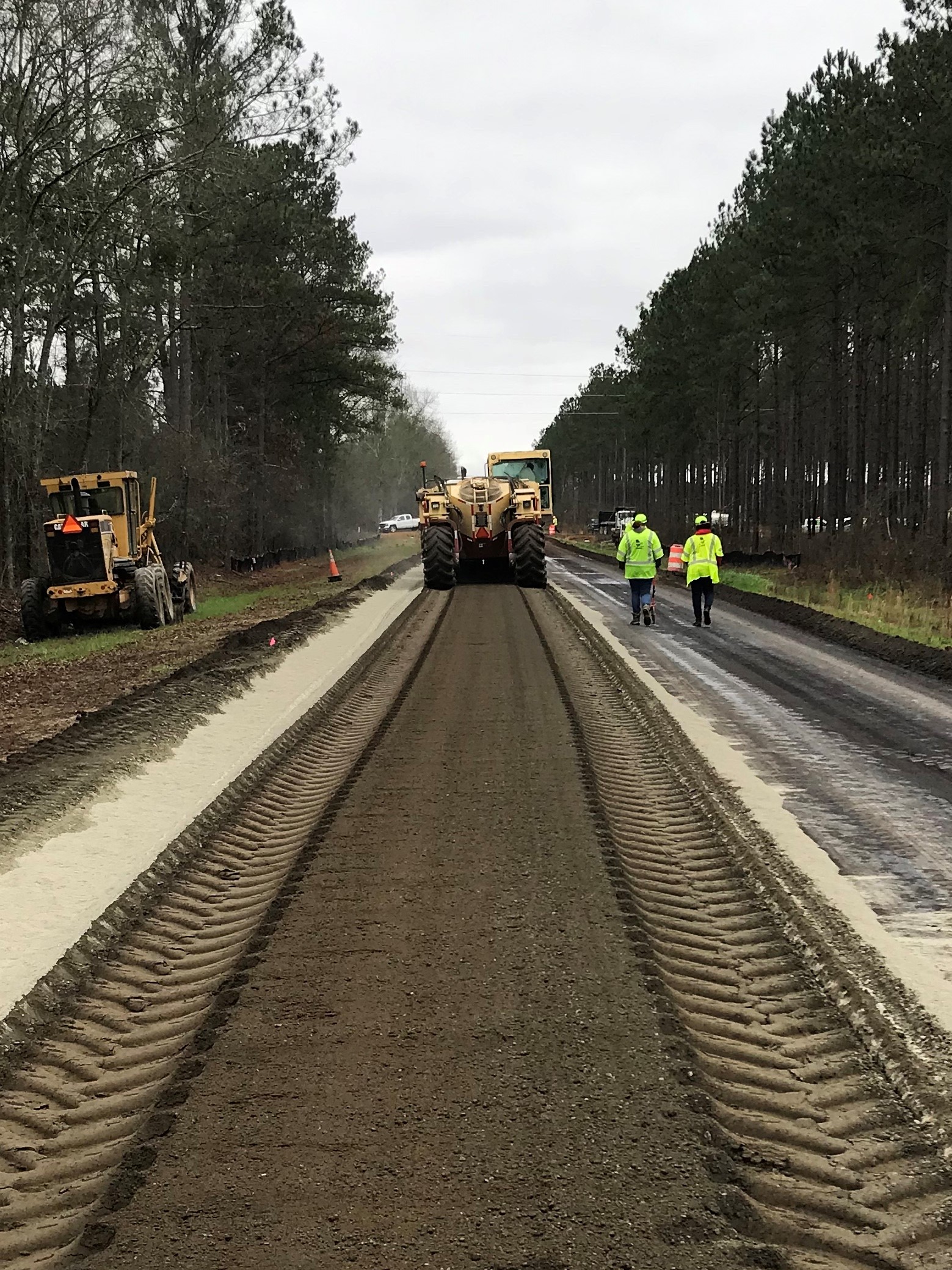
Improving sustainable practices in road construction and rehabilitation is important to an overall project. FDR reuses up to 100% of existing materials and aligns with sustainable practices by minimizing the consumption of new materials and reducing waste generation. Using existing materials decreases the demand for new aggregates, conserves natural resources, and eliminates transportation and disposal of old materials. Adopting FDR can minimize carbon emissions, reduce energy consumption, and promote a more sustainable approach to road rehabilitation.
By recycling existing pavement materials and adding stabilizing additives, FDR provides a cost-effective, environmentally sustainable, and durable solution for aging roadways. Its ability to reduce costs, improve performance, and minimize disruption makes FDR a valuable option for transportation agencies seeking efficient and sustainable solutions to meet their infrastructure challenges.
S&ME FDR Mix Design Services
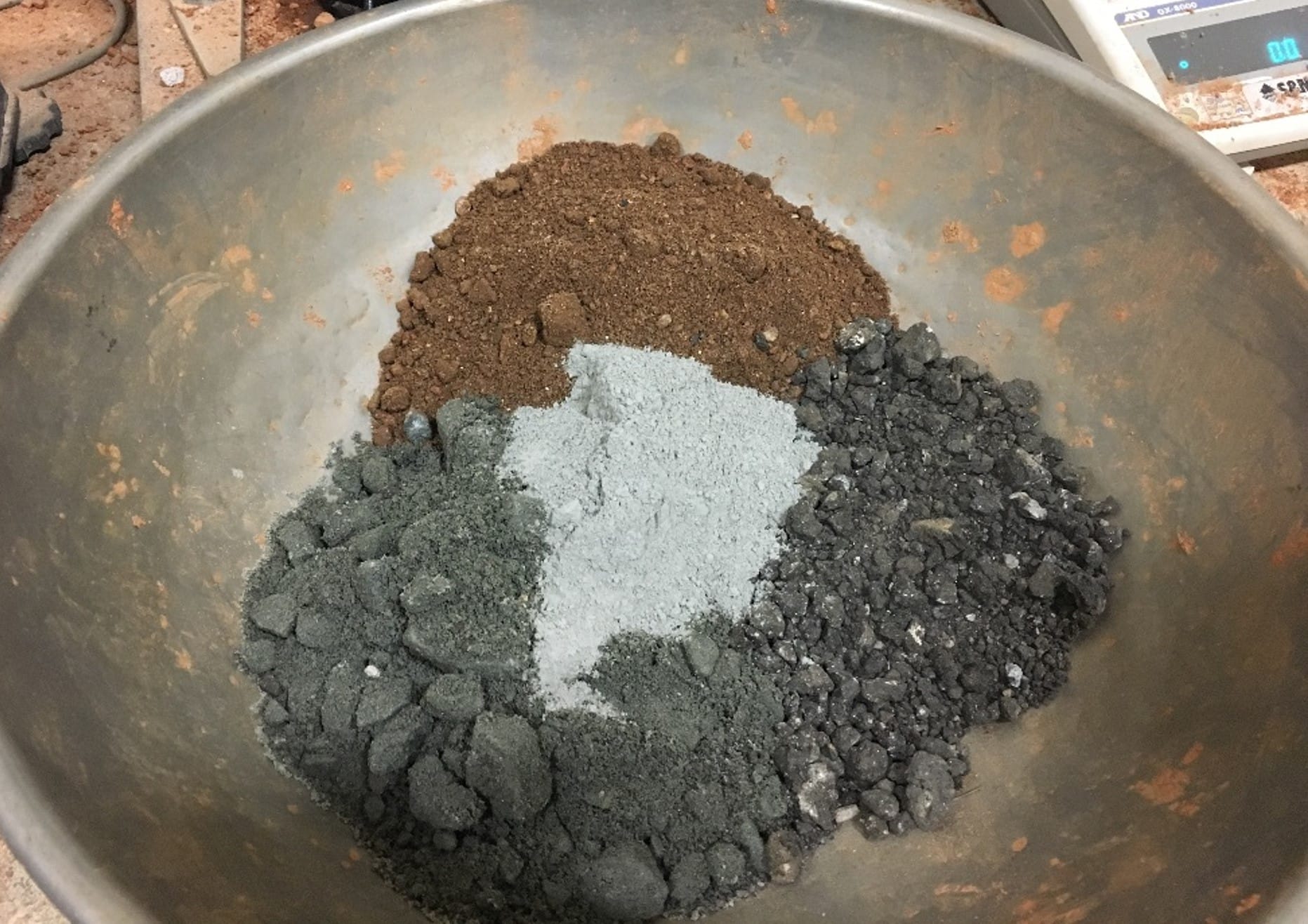
Materials samples at S&ME’s asphalt laboratory
Existing pavement component thickness and subgrade soil conditions will vary from project to project. Therefore, the number of additives needed to produce a durable road base will also vary. When the FDR repair strategy is implemented, in-place thicknesses and materials must be obtained.
This is typically accomplished by performing pavement coring and shallow subsurface exploration at regular intervals in the existing pavement sections. Samples are obtained during this process and transported to the laboratory for performance of FDR mix designs.
The shallow subsurface information and materials obtained during pavement coring activities guide the designer to recreate a blend of the sampled materials in the laboratory representing the expected conditions during FDR construction. Varying amounts of additives are introduced to this laboratory blend and compressive strength specimens are molded. The results of laboratory compressive strength testing indicate the quantity of additives that need to be introduced during construction to create a durable FDR base.
S&ME Materials Testing Services
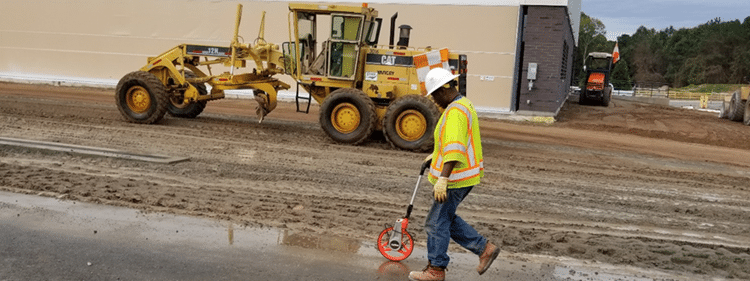
S&ME technician measuring the area of FDR base construction.
As with any pavement construction project, it is important that the materials used are tested for quality. Materials testing on most pavement projects involve in-place density testing, thickness measurements, subgrade evaluations, etc. Along with these typical test procedures, additional testing specific to FDR construction is often required. These include observing and documenting additive spread rates and moisture addition, observing that the materials are adequately pulverized, recording that the proper mixing depth is achieved, and field-molding specimens (or obtaining FDR base cores) for laboratory compressive strength testing.
S&ME FDR Projects
Taylor Road
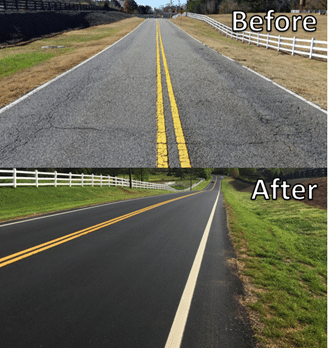
Taylor Road Project before and after FDR services.
FDR base construction was used to upgrade and create a paved shoulder on Taylor Road in Milton, Georgia. S&ME provided pavement design, laboratory FDR mix design, and construction materials testing services for this project.
Traditional methods of road reconstruction were forecasted to take several months; however, this approximate 1.3-mile stretch of Taylor Road was reconstructed over a period of about 10 days with the FDR repair method.
S&ME performed falling weight deflectometer (FWD) testing before and after FDR construction. These test results indicated a significant improvement in subgrade strength and increased service life for the roadway.
Coweta County FDR
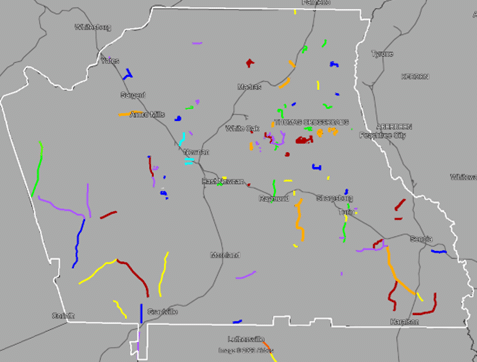
Visual map of Coweta County FDR roadway reconstruction projects
S&ME has served as the FDR mix design consultant and materials testing firm for six consecutive years (from 2018 to 2023) of Coweta County-funded FDR roadway reconstruction projects. Services under these contracts have included FDR repairs to nearly 100 centerline miles of residential, rural, and collector roads maintained by the County.
Contact Us
For more information on S&ME’s FDR services, please contact Shea Vincent, PE.