July 16, 2025
If you’ve ever talked with an architect, engineer, or contractor you may find they use a lot of letters in their lingo. This campaign is an effort to demystify some of the commonly used acronyms in the Architecture, Engineering, and Construction (A/E/C) industry, what they mean, and why they are important.

What is a Certified Welding Inspector (CWI)?
A Certified Welding Inspector (CWI) is a professional who is qualified to inspect the quality and safety of welded structures and components. Certified by organizations like the American Welding Society (AWS), a CWI is responsible for verifying that welding work meets industry codes, standards, and project specifications. Their duties often include reviewing blueprints, conducting visual inspections, performing tests, and documenting compliance. CWIs play a critical role in industries in construction, manufacturing, and shipbuilding, where strong, reliable welds are essential for structural integrity and safety.
Meet Certified Welding Inspector, Carlos Ybarra
We spoke with Carlos Ybarra, a Metals Technician at S&ME, based in Raleigh, North Carolina, to learn more about his career and experience. He has 10 years of experience, spending time both in welding and in the field.
What led you to pursue certification as a CWI, and how has the role evolved for you over time?
“I’ve always found great satisfaction in being a welder and working within the welding field. It has been rewarding to pass on the knowledge I gained from seasoned professionals to younger welders, helping them improve their skills and the quality of their work just as the older generation did for me. To further extend my impact, I pursued my Certified Welding Inspector (CWI) credential. This role allows me to not only hold welders to industry standards but also guide them through the intricacies of American Welding Society (AWS) and American Society of Mechanical Engineers (ASME) codes.”
Can you walk us through a typical day in your role?
“There’s no typical day in my current role, and that’s one of the aspects I enjoy most. Each day presents new challenges, requiring a deep understanding of codes, specifications, and how to interpret them accurately. The most critical aspect of my work is ensuring that the welds meet the required standards and specifications, verifying everything against the correct codes.”
What welding codes or standards do you work with most often, and how do you stay current with updates or changes?
“The most often used code for steel erection is AWS D1.1 M: 2025 Structural Welding Code – Steel. This was just updated from 2020 to the current 2025. Staying active within the AWS community and having great group leadership helps keep you current and up-to-date on changes.”
What’s the most technically challenging project you’ve worked on, and how did you approach it?
“I assisted the NCDOT with the development of a welding procedure specification (WPS) and welder performance qualification record (WPQR) for AWS D1.2 Aluminum and ASME BPVC Section IX CO/NI brazing. This task presented a unique challenge as I was simultaneously guiding both the welders and brazers through the intricacies of two distinct codes. To ensure clarity and precision, I carefully reviewed each requirement, consulted with a Senior Metals Technician for further insight, and then communicated the expectations clearly to the team before work began. This approach helped align everyone with the specific standards and ensured a smooth execution of the project.”
What are the most common welding defects you encounter in the field, and how do you identify and address them?
“The most common weld defect is undercut. Undercut is when the welding arc strikes a portion of the base material and is not filled with filler metal. For visual inspection, utilizing a light at several light angles will create shadows on the undercut areas. Once the discrepancy is noted, the code must be referenced to determine if it is an acceptable or rejectable discrepancy.”
How do you determine the most appropriate NDT (non-destructive testing) methods for a given job?
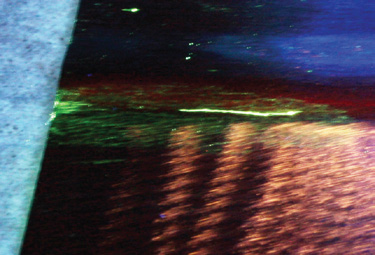
Penetrant testing
“The selection of the most appropriate Non-Destructive Testing (NDT) method is influenced by several key factors, including code requirements, cost considerations, and accessibility. Ultimately, a balance of these factors ensures the most effective and efficient NDT solution, assuring the integrity of the weld while meeting project constraints and regulatory standards.”
How does your work contribute to the overall quality and safety of projects?
“My work contributes to the overall quality of projects by keeping the product to the required code and standards. It gives the customer what is expected to keep the structure and components safe and what they paid for.”
What’s your favorite part of the job?
“I enjoy the spontaneity that comes with every week. One week, I might be conducting penetrant testing on welds, inspecting above-ground tanks, and performing fireproofing adhesion/cohesion tests; all in the same span of time. It keeps the work dynamic and engaging.”
What other inspection certifications do you hold? How has becoming a CWI led to you attaining other certifications?
“In addition to my CWI, I hold several other certifications, including SP001 Above Ground Storage Tank Inspector, VT II, UTT, ICC Spray Applied Fireproofing Special Inspector, and OSHA 30. Becoming a Certified Welding Inspector has not only validated my commitment to the industry but also opened doors to additional certifications. It has helped me expand my skill set and versatility, enabling me to take on a broader range of responsibilities and contribute more effectively across various inspection disciplines.”
Do you have a favorite welding project or structure you’ve helped inspect that you’re particularly proud of?
“I find a great deal of satisfaction in working on water towers. I’ve always had an appreciation for heights, and there’s something uniquely rewarding about being on top of a water tower. These structures are vital pieces of infrastructure, and it’s fulfilling to stand on the roof, taking in the view of the area they serve. It gives a sense of connection to the broader community and the essential role these towers play in daily life.”
What advice would you give someone considering becoming a CWI?
“Don’t just make the bare minimum prerequisites; invest in learning and studying the welding field. When you get to that point in your career, I would recommend looking into the Hobart Institute of Welding in Troy, Ohio. They have a fantastic AWS-CWI preparation examination program.”